5 Questions to Answer Before Choosing a CNC Guideway
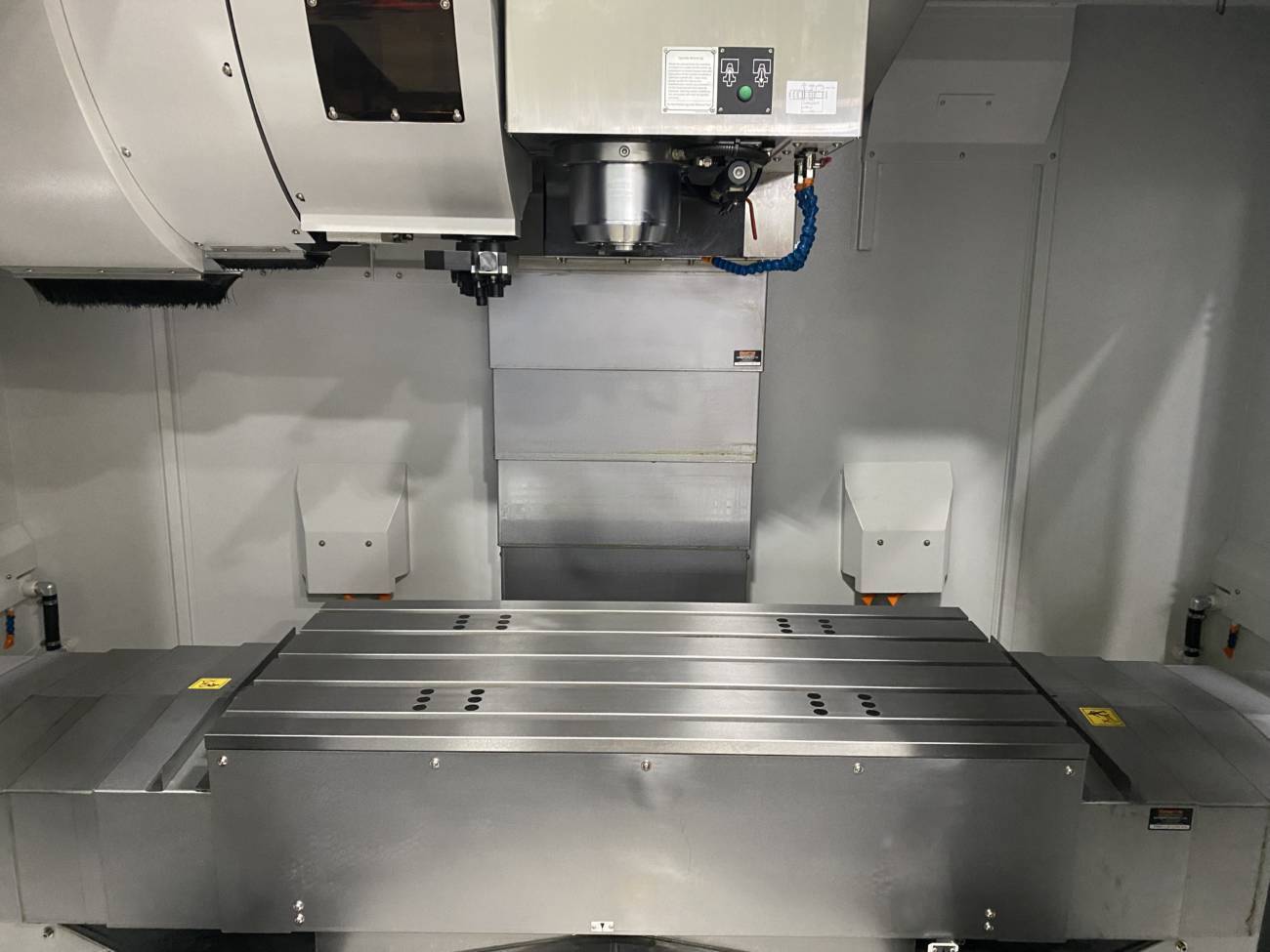
“It depends.”
These are two of the most common words you’ll hear if you ask an operator which CNC machine guideway assembly to use.
What is a Guideway?
A guideway is a CNC machine component that determines how a cutting element or table moves along the axes. In the broadest terms, guideways comprise a carriage attached to a rail, driving the cutting tool or table along a set path.
Guideways are one of the most critical aspects of a machine tool. The type of guideway on a machine will dictate and influence other machine tool specifications, such as maximum load capacity, speed, rigidity, precision, accuracy, and cost.
Given a guideway’s foundational role on a CNC machine, establishing the required guideway is a good starting point when analyzing choices for a new machine tool. Generally, your choices fall into three categories: linear, box, and hybrid guideways.
- Linear guideways have spherical ball bearings or cylindrical rollers in a carriage to slide across the rail.
- Box guideways have rectangular bearing pads on the carriage’s interior that make contact with the rail, allowing the housing to move along the rail.
- Hybrid guideways, as the name implies, use both linear and box-way guides. Generally, this means the Z-axis on the machine is a box type, while the X- and Y-axes are linear.
5 Questions to Determine the Best Guideway for Your Production
While there’s no objective “best” type of guideway for all machining applications, here are 5 helpful questions and insights from our experts to help you determine which kind of guideway best fits your production needs:
1. What are you cutting?
If you’re cutting strong and hard metals such as titanium, tungsten, chromium, or certain alloyed steels, you will need a machine with more cutting force, torque, and rigidity.
Box-type carriages have large, rectangular mating surfaces that glide along the rail, creating more surface and contact area than linear motion machines.
“With a larger surface area and contact points on the carriage, you will get more rigidity and heavier cuts,” said Bernard Otto, Methods’ Director of Technical Support and product manager for KIWA and OKK machine tools.
“Many hybrid machines have a box-type guideway on the Z-axis and linear guideways on the X- and Y-axes. Utilizing a box-type guideway on the Z-axis gives hybrid machines more rigidity where it counts, while the linear guides on the X- and Y-axes provide more fluid speed and movement compared to box-type guideways. You really don’t need a box-way machine if you’re cutting aluminum or low-strength steel, it’s more power than you need,” Otto said.
While a box-way machine can cut aluminum or other softer metals, it’s just not the best tool for the best job. Box-way machines generally involve more hand-scraping on mating surfaces and are therefore more costly than linear-guideway machines. It wouldn’t be cost-effective to pay for something you’re not going to use.
2. What do you need more — Speed or Rigidity?
The round bearings of linear guideways let the carriage glide across the rail, making them faster than box-type guideways.
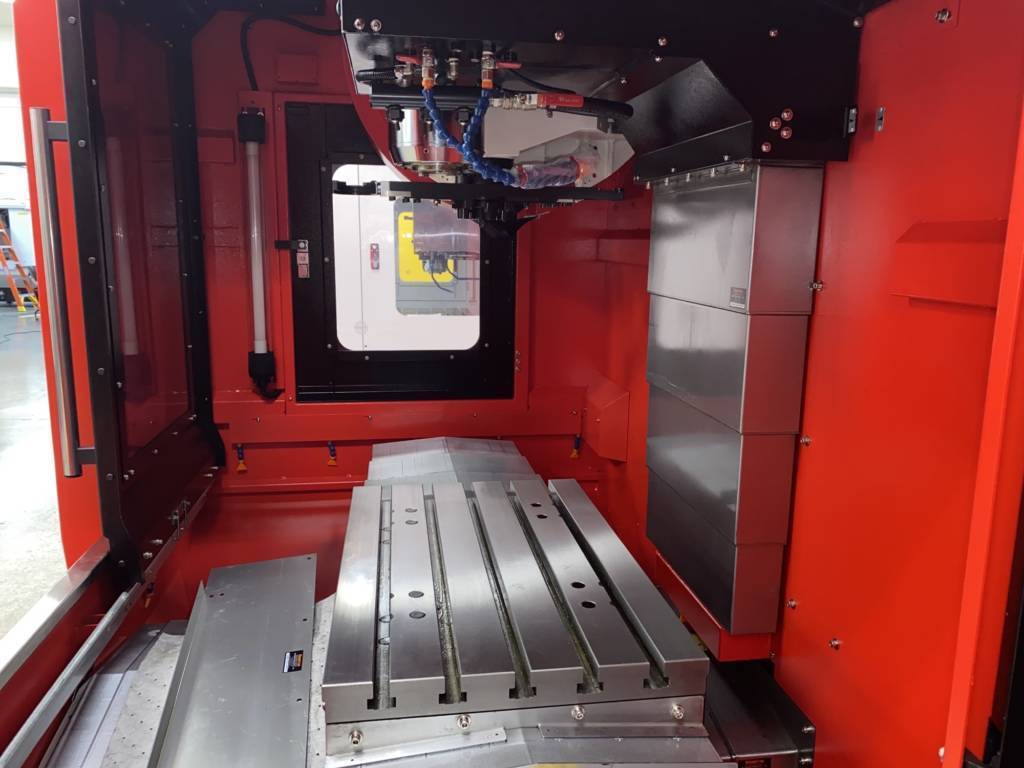
The Methods MV600H has a box guideway on the Z axis and cylindrical roller guideways on the X and Y axes.
“When you’re cutting elements and tables move faster, you’ll be able to complete more jobs in less time,” said Darren Wall, Product Manager of the Methods brand of machining centers. “Shaving seconds off a job is one of the most straightforward ways to reduce your costs and see the return on your investment.”
Linear guideways enable faster rapid motions compared to box-way machines. Rapids — the maximum speed the table and cutting element can move along an axis — are important metrics when positioning tools or changing cutting positions. Essentially, the faster your rapids, the shorter your cycle times.
Smaller carriages on linear guideways achieve faster rapids for quicker tooling and cutting positions compared to box-type guideways.
“Linear guideway machines are going to give you faster rapids, quicker tool positioning, and better throughput compared to box-way machines,” added Kevin Sarro, Methods’ Director of FANUC America products.
In exchange for slower movement, box-way machines offer more rigidity. Box-way machines absorb more vibrations since there’s more direct contact between the carriage and rail, so you can repeat the same processes without losing any precision.
“You get a more rigid cut generally at the cost of speed,” Otto said. “And, a lot of box-way manufacturers compensate for this friction using self-lubricating materials like Turcite and Rulon, making the movement more fluid.”
3. Does your production floor have any size constraints?
At first glance, this is a simple question. If a machine fits, it fits. However, shops should consider how new equipment fits into their plans for future growth.
- Does purchasing a larger machine now prohibit you from adding another machine down the line?
- Can two smaller machines take the place of one larger machine?
- How will new machinery affect your output in a month, a year, or five years?
Since box-way machines are designed for larger applications, they typically take up more space than machines with linear guideways.
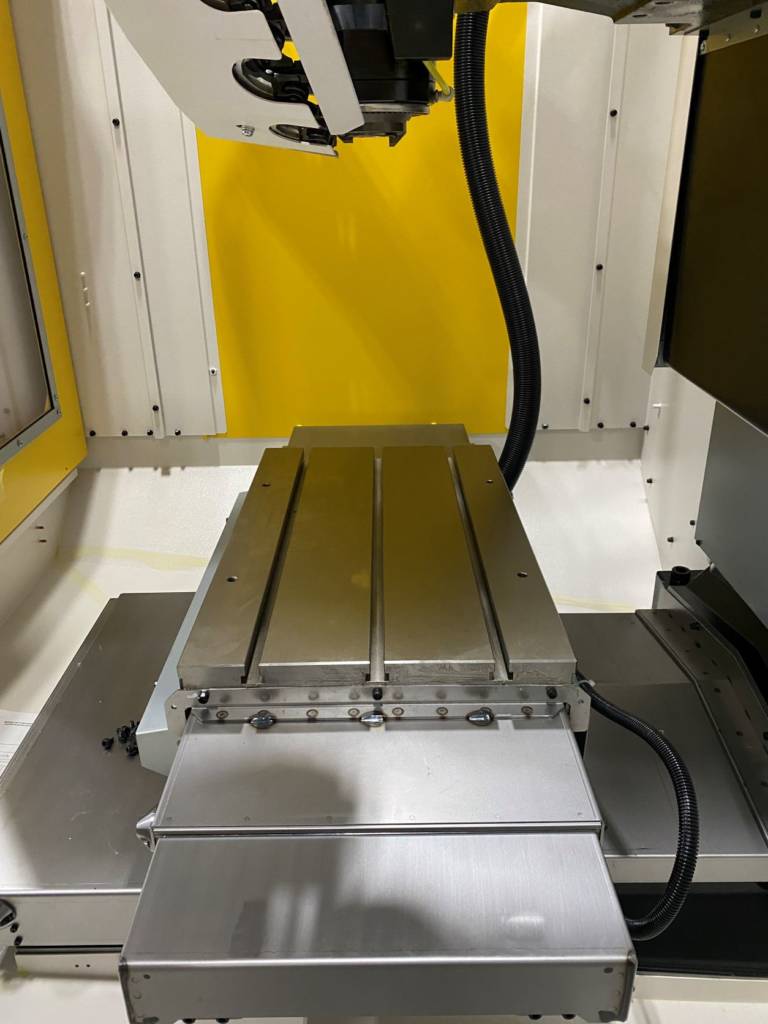
FANUC RoboDrills feature a linear guideway
“Floor space can be a tough nut to crack, but it’s a worthwhile effort,” Sarro said. “Linear guideways contribute to two of RoboDrill’s biggest strengths – its compact size and its capacity for high-speed machining. You have to examine how much production capacity you want to get from every inch of floor space and figure out how many machines could fit in a specific area.”
However, box-way machines pull their weight – and footprint – on the shop floor. They are better at roughing and cutting through tough-to-machine metals in most applications. These qualities mean your shop may be capable of taking on more profitable jobs when you’re looking to machine alloys used in demanding applications, such as the aerospace, medical, and defense industries.
4. Are you machining big or heavy parts?
This is not a trick question. If the answer is “yes,” box-way or hybrid machines should be at the top of your list.
“Since box-way machines have more contact between the carriage and rail, they can handle heavier workloads than other guideway types,” Wall said. “They also have more rigidity, allowing you remove more material with each pass.”
Box-way machines generally involve more craftsmanship. The mating surfaces on the carriage that move along the rail are often hand-scraped. Hand scraping creates a flat surface within millionths of an inch and up to 10 contact points per square inch. That level of contact and flatness absorbs vibrations better, making a more precise, rigid machine.
5. Do you need the “best of both worlds”?
While hybrid machines aren’t quite as fast as linear guideway platforms or as rigid as box-way machines, they strike an even balance between the two. Most hybrid machines have box-way guideways in the Z-axis, and a linear construction in the X- and Y-axes.
That’s part of the reason why hybrid machines are so appealing.
Trading off speed for higher rigidity in the Z-axis – where the tool does the cutting – is an excellent way to balance rigidity with speed. Similarly, having higher speeds in the X- and Y-axes allows operators to reach other parts of the workpiece faster.
“You really have the best of both worlds,” Wall said. “Once you realize the benefits of using both types of guideway in one machine, you’ll ask yourself why you would want to use anything else.”
Want to find the right CNC solution for your business? Contact the experts at Methods.