51
VisionGauge
700 Series
The 700 Series VisionGauge® Digital Optical Comparator 5-Axis Inspection and Measurement Systems are the perfect solution for checking EDM- and Laser-Drilled Holes and Slots.
There are many reasons why the VisionGauge® Digital Optical Comparator is widely used by manufacturers across a broad range of industries (including aerospace and power generation) to check EDM- and LASER-drilled drilled holes and slots:
- Automatically verify hole presence & accurately measure hole location
- Supports both round and shaped holes
- 5 axes of motion (X, Y, Z, Rotary, Tilt) to properly view parts from all sides & angles
- Quickly, easily and accurately inspect 100% of the holes on your parts
- Robust shop floor design
- Can output the hole offsets which can be used to modify EDM drilling programs
- Mounting system allows your parts to go directly from the EDM drilling machine to the inspection system without re-fixturing (quick & easy and also minimizes stack-up error, etc…)
- The system can be supplied with the same working envelope as your EDM drill. If you can drill it, we can check it!
- Holes can be checked either one at a time, looking straight down each hole’s nominal axis (ideal for coated parts, to minimize errors due to coating thickness variations) or multiple holes can be checked at once, viewing them at an angle (which is even faster and well suited for uncoated parts or parts with a uniform coating thickness)
- The system has an extended depth of field, so that everything is perfectly in focus regardless of the part’s geometry (even in areas of very high curvature) as well as a very long working distance (so that there is lots of clearance between the part and the entire optical system to comfortably accommodate large and unusually-shaped parts)
- Extremely powerful “adaptive” feature-detection software tools are able to accurately find and locate EDM-drilled holes on different surfaces, with different reflectivity, at different viewing angles, etc…
- Specialized software tools are especially well suited to deal with burrs and splatter
- Automatically create reports and collect measurements, statistics, images and other data for complete documentation
- Fast and intuitive “operator review” mode allows the operator to quickly revisit out-of-tolerance areas, etc…
- The ideal system for inspection and measurement of cooling holes on aircraft engine and IGT (Industrial Gas Turbine) components (blades, vanes, heat shields, shrouds, etc.). Parts can be either (ceramic) coated or uncoated.
The VisionGauge® Digital Optical Comparator 5-Axis Inspection and Measurement Systems are a very cost-effective, perfectly adapted solution for checking EDM and LASER-drilled drilled holes and slots. It is rapidly becoming the new standard in the industry!
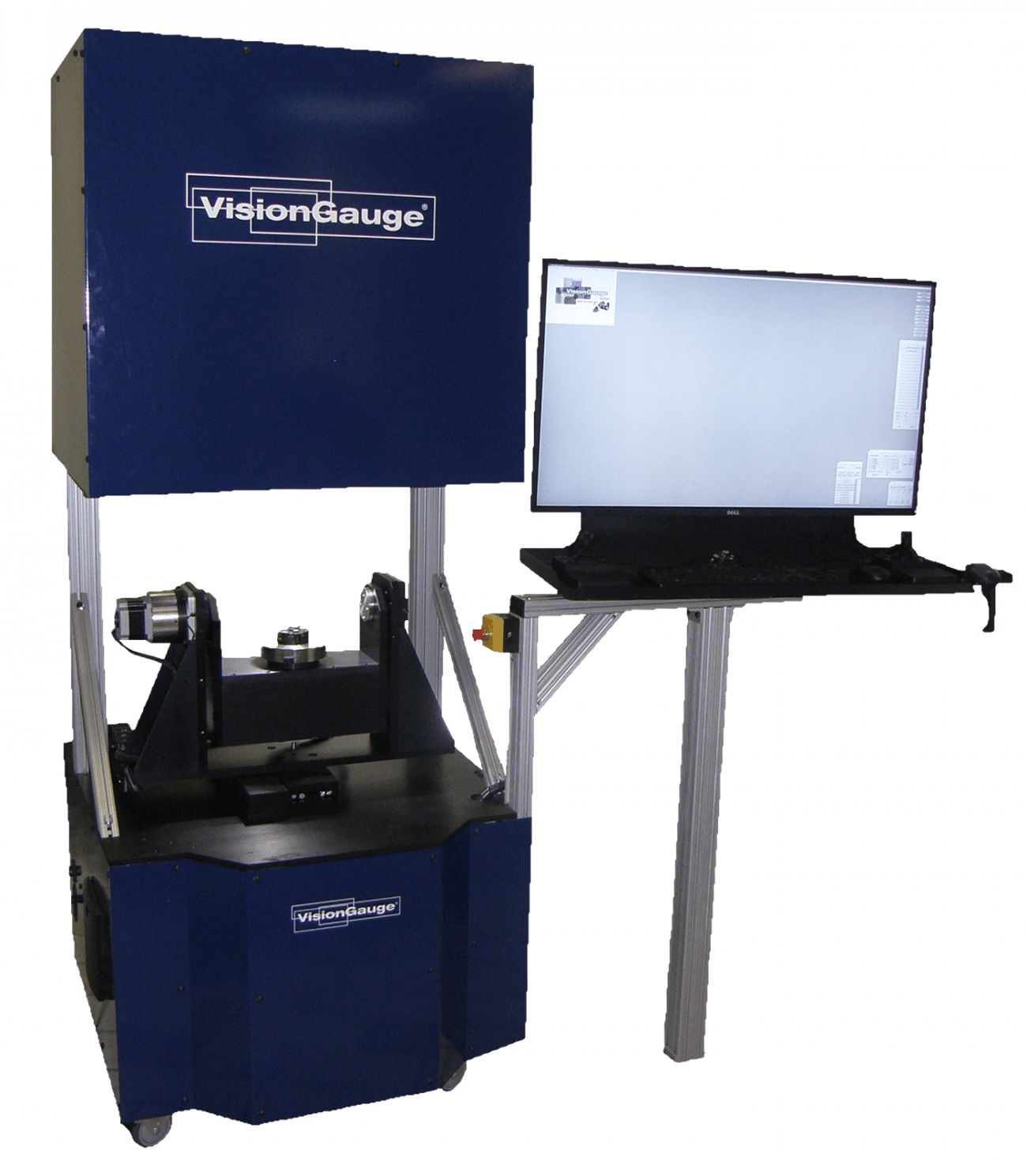
Product Details
Features & Benefits
- 5 axes of motion (X, Y, Z, Rotary, Tilt) to properly view parts from all sides & angles
- Fully-automated operation
- No operator-to-operator variation
- Easy to program (can use your CAD data directly)
- Fast, accurate, & easy-to-use
- Extensive set of measurement tools
- Straightforward operator interface: barcode-reader and joystick
- Intuitive software
- Able to carry out full 6-point iterative alignment
- Patented & patent-pending technology
- Powerful & innovative software tools for robust feature detection
- Sharp, clear, & ultra-high resolution image!
- Ultra-bright all-LED computer-controlled multi-angle and multi-quadrant illumination is standard!
- High-resolution precision optics to make out very fine details with great clarity
- Extended optical depth of field and extended working distance for maximum flexibility!
- Automatically create reports and collect measurements, statistics, images, and other data for complete documentation
- Automatic image & data collection with built-in SPC and data-exchange capabilities
- Ideal for aircraft engine and gas turbine blade cooling holes inspection and measurement.
- Fast and intuitive “operator review” mode to quickly revisit out-of-tolerance areas
- Robust shop-floor design
Technical Data
- Number of motorized axes 5
- (X, Y, Z, Tilt & Rotary)
- Standard Travels (X, Y, Z axis)
- 12" (300 mm) / 24" (600 mm)
- All axes have closed loop encoder feedback
- X-axis encoder resolution = 0.25 μm Y-axis encoder resolution = 0.25 μm Z-axis encoder resolution = 0.25 μm A-axis encoder resolution = 0.005° B-axis encoder resolution = 0.005°
- Stage movement
- X-, Y- and Z- axes: high-accuracy preloaded crossed-roller movement precision worm gear with high-accuracy preloaded crossed-roller movement
- End-of-travel limits
- Optical (for high repeatability)
- Mounting System
- System 3R Macro Chuck (p/n 3R-600.24-S) (Other mounting systems available upon request)
- High-resolution optical system
- 20X equivalent optical magnification (approx.) Working distance = 9.0” (228 mm) Depth-of-field = 1.8” (45 mm) Field of view = 1.7” (43mm) x 1.2” (30 mm) = 2.1” (53 mm) Ø Optical system accuracy: better than +/- 0.00015” (4 μm)
- General-purpose dual source reflected (i.e. front) LED illumination
- Ultra-bright, all-LED based (for stable and repeatable illumination conditions & results as well as long life) Fully computer-controlled & programmable Produces very high brightness to easily handle even difficult-to-image areas The system’s dual-source illumination module provides lighting at different angles of incidence (i.e. both near-vertical and low-oblique) for wide applicability across a very broad range of part geometries.
- VisionGauge® Software
- Powerful and easy-to-use Intuitive, windows-based graphical user interface (i.e. “point & click”) Full 5-axis transforms Advanced software corrections with full 3D mapping across the system’s entire work envelope Includes a wide range of powerful inspection and measurement tools Robust & field-proven, with a broad installed base (over 3500 license in use worldwide)
- 5-axis corrections
- Chuck offset, fixture height and fixture center-of-rotation (X,Y) offset
- Software feature-detection tools
- Extremely powerful “adaptive” software feature-detection tools are able to accurately find and locate features of interest (such as EDM-drilled holes) on different surfaces, with different reflectivity, at different viewing angles, etc.
- Digital Read-Out (i.e. DRO)
- Yes (on-screen)
- Auto-focus
- Yes (with programmable region-of-interest)
- Camera
- High-resolution, digital (9 Megapixel)
- Live video “refresh”
- Real-time
- Real-time mathematical image processing, enhancement and correction
- Yes
- Multi-monitor display
- Yes
- Extended set of high-accuracy measurement tools
- Yes
- Sub-pixel accurate edge detection
- Yes
- Image annotation tools
- Yes
- Built-in SPC capabilities, with automatic numerical charts & PASS / FAIL graphs
- Yes
- Automatic data export to Excel™
- Yes
- Automatic data export to other applications
- Yes (through Windows™ DDE and other mechanisms)
- Built-in Dynamic Data Exchange (DDE) support
- Yes
- Easy file data import & export
- Yes
- Automatic operation & program launch using the system’s barcode reader
- Yes
- Barcode reader Honeywell, industrial grade Supervisor-level / operator level password protection
- Yes
- Operating System
- Windows™ 7
- Built-in "F1 Help"
- Yes
- Power requirements
- 110V, 15 Amp
- Operating Temperature
- 10 °C - 30 °C
- Clear and easy-to-use documentation (both printed and electronic "pdf" format)
- Yes
- Support (by phone, fax & email)
- Included for a full year
- Free software updates
- Included for a full year
- Warranty
- 1 year (complete)
Videos
Sorry, there are no videos for this machine.